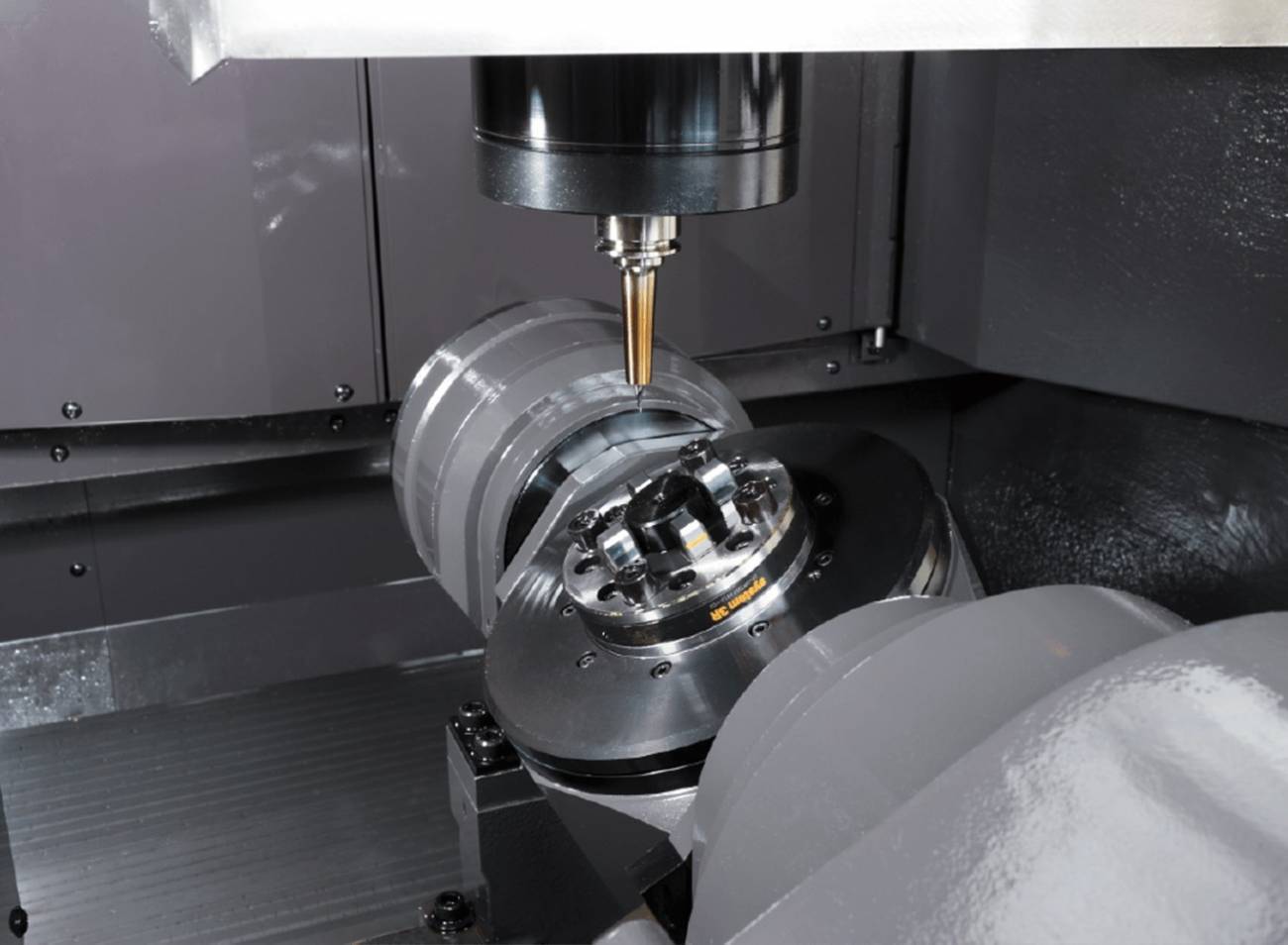
Case Study
X-Cell Tool & Mold, Inc.
RequestInformation
Problem
Manufacturing plastic injection molds is a demanding, time-consuming process. X-Cell's General Manager, James Cummings, wanted a new way to create multi-cavity plastic injection molds with precise tolerances while lowering cycle times.
Solution
Cummings installed a five-axis CNC machine, a YASDA YMC430 RT10, as well as a YASDA YMC650, both of which were automated.
Results
The machines produce exact tolerances and a high level of precision in record time. X-Cell was able to produce 4 two-shot molds for ventilator components in 10 weeks, thanks to the accuracy of the 5-axis YASDA machines and automation systems.
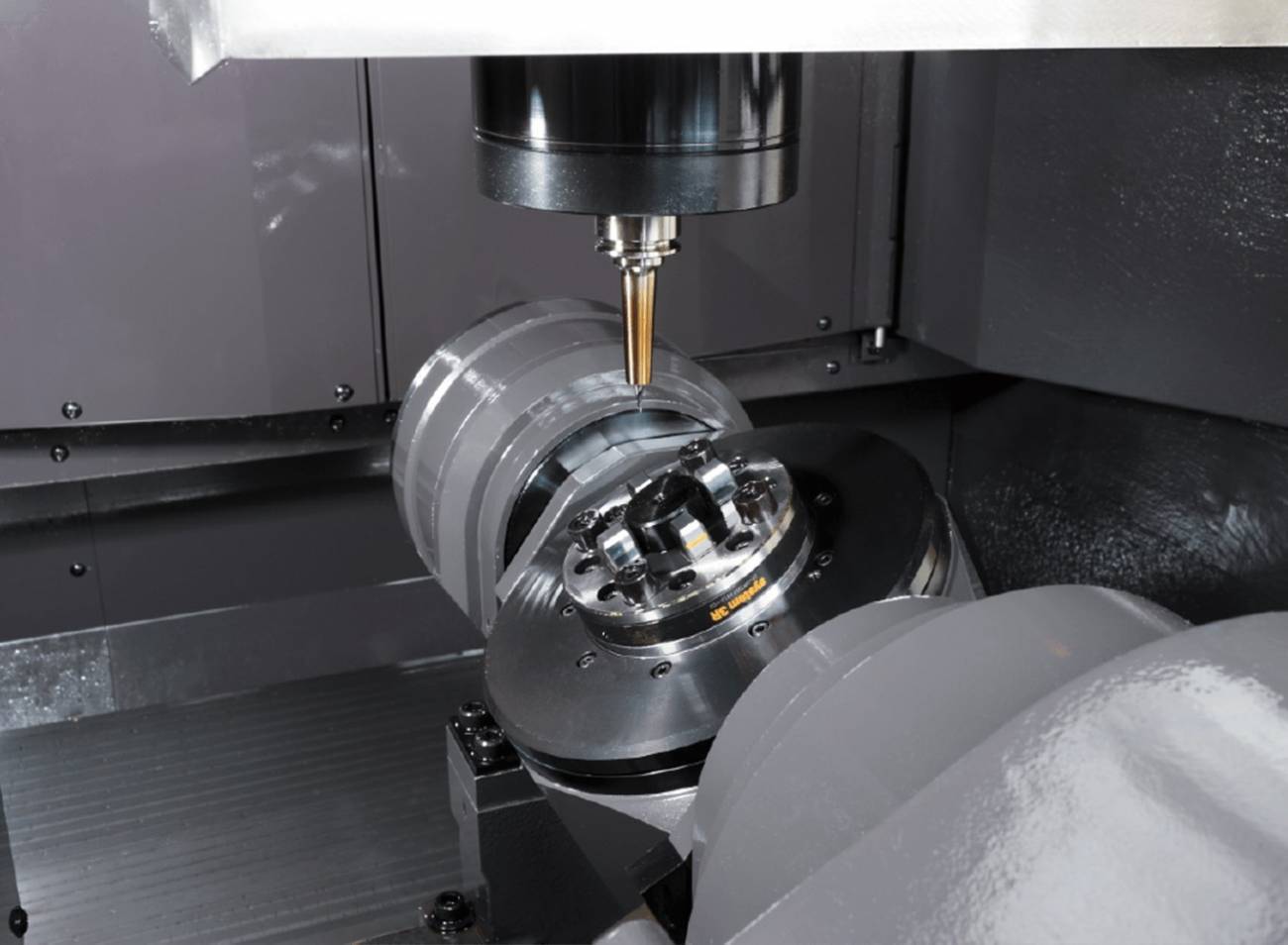