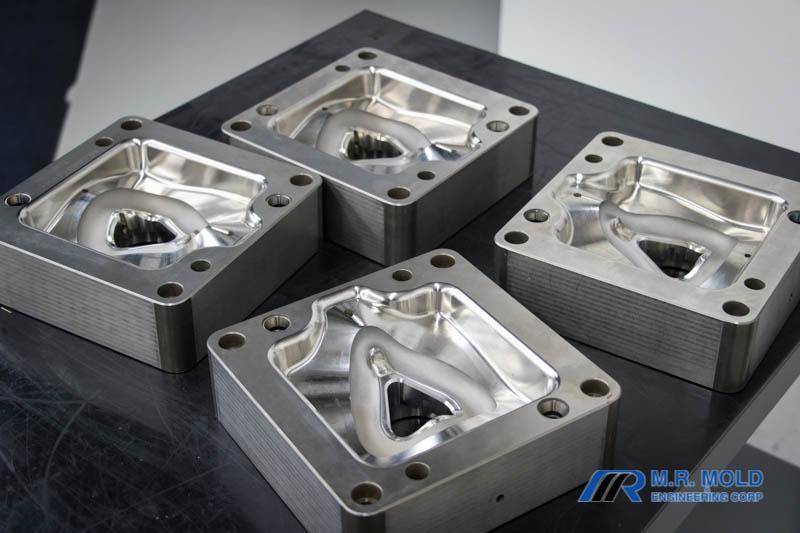
Case Study
Five-Axis Machining Carves a Better Path for Mold Maker
RequestInformation
Problem
Liquid Silicone Rubber (LSR) is a dynamic material with a wide ranging temperature tolerance and flexibility to make countless shapes. After years spent on their 3-axis milling machines, the team at M.R. Mold and Engineering realized to remain competitive, they needed to elevate their machining so they could reduce the number of operations and processing time of each part.
Solution
After engaging industry colleagues for their perspective, the M.R. Mold team reached out to Methods regarding the YASDA YBM Vi40 5-axis jig boring-milling machine. With the machining center in house, M.R. Mold gained tighter tolerances, their number of operations, and cut overall setups for an improved end-to-end machining process.
Results
- 75% reduction on hours per stress ball cavity
- 40-hour reduction in setups
- 40-hour reduction in machining and polishing time
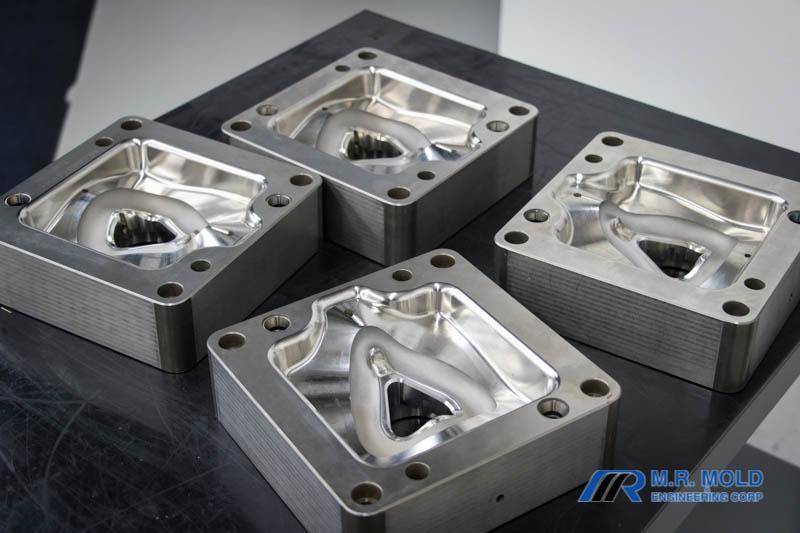
Conquering Liquid Silicone Rubber
Liquid Silicone Rubber (LSR) has a low compression set and fast cure cycles. Coupled with great stability, it can resist extreme temperatures of heat and cold. This makes it ideally suited for the production of parts for the medical industry, where quality and accuracy are crucial.
LSR remains flexible and elastic down to -70°F and retains its properties up to 450°F. Many thermoplastic materials can be molded with limited flash using fit specifications between inserts of up to 0.002 in. However, LSRs will often flash even with fit requirements as tight as 0.0001 of an inch or less. This necessitates a different level of engineering, machining, processing precision and expertise.
M.R. Mold and Engineering Corporation is known for its unprecedented expertise in LSR, as well as leaders in the education of the silicone industry. Founded in 1985 by Rick Finnie, M.R. Mold opened as a two-person shop. Today, M.R. Mold boasts 30 employees and a 15,000-plus square foot facility complete with a 4,000 sq. ft. Technology Center featuring six molding machines and automation for customer required samplings and runoffs.
Fit or Flash: 3-Axis Milling Challenges
Over the years, M.R. Mold invested in several CNC mills, as well as Wire EDM and Sinker EDM. The company’s core customers require close tolerances, little to no flash, and cosmetically perfect parts. Those results proved difficult to achieve with conventional CNC 3-axis machines.
“In our industry niche, we were machining complex 3D cores and cavities on conventional 3-axis mills where feeds, speeds and surface finish were being compromised. The EDM process was often required as the 3-axis mills were unable to accurately perform the needed machining operations,” said Finnie. “Additionally, 3-axis machining sometimes required as many as five setups for some of the complex geometries. This process proved to be inefficient, wasted valuable time and introduced errors with each new operation, which compromised the accuracy of the work.”
“Silicone flashes very easily and medical components have critical tolerances and minimal flash allowances,” Finnie added. “Achieving a high level of accuracy on complex geometries using 3-axis equipment was a huge burden to overcome and led to multiple reworks once molds were sampled and evaluated in the press. The main culprit — parting line flash.”
Finnie knew the time had come to make an investment in a 5-axis machine; especially since one of the company’s largest customers had close tolerance work that required a high level of accuracy.
The YASDA Solution
Finnie spoke to several of his contacts in the moldmaking industry who had purchased other 5-axis machines, but they were not accurate enough for what he needed. Then he spoke to another friend, and moldmaking expert, who had invested in a YASDA.
YASDA’s superior reputation in the industry as an extremely accurate machine lends itself to the nickname, “the mother
of all machines.”
“I had a candid conversation with my friend about YASDA. He said, ‘If you want to take off a tenth, that YASDA will do it all day,’” Finnie said. “He gave me his reassurance the YASDA machine would hold the extreme tolerances required for molding silicone.”
At Methods’ headquarters in Sudbury, Mass., there was the exact YASDA machine that Finnie needed — the YASDA YBM Vi40.
The YASDA YBM Vi40 5-axis Vertical CNC Jig Boring-Milling Machine offered the exceptionally high accuracy M.R. Mold needed. The YBM Vi40 includes a simultaneous 5-axis cone machining circularity of 2.32 µm, 0.89 µm positioning accuracy of the Y-axis, and indexing accuracies of ± 0.50 sec on the B-axis and ± 0.20 sec on the C-axis.
A 24,000 RPM, 40-taper direct-drive spindle offers a high degree of precision throughout the entire speed range. To reduce thermal distortion and achieve the highest precision 5-axis machining, including over long production runs, the YBM Vi40 features a thermal distortion stabilizing system where the X-Y-Z axes and two rotational axes (B/C) are maintained to +/- 0.2 degrees C to shop ambient.
Circulating temperature-controlled oil through the machine minimizes thermal displacement of each axis. A highly rigid and accurate rotary B/C-axis mounted on the Y-axis machine bed controls movement and offers extraordinary machining stability, even when adding up to 400 pounds of weight including the fixture and part.
Proof is in the Molding
“Seventy percent of the molds we build have complex geometry, and the capabilities of the YASDA 5-axis enabled us to increase our already finite capabilities,” said Finnie. “The YBM Vi40 produces surface finishes which meet extremely tight tolerances and do not require secondary finishing operations, making complete net shape machining in one operation possible. In addition, the machine offers 5-sided machining in a single set-up.”
The machine saved M.R. Mold 40 extra set-up hours and 40 hours of machining and polishing time on a recent mold that was built.
“We spend less time relieving cutters because the machine rotates with the cut, so the cutters stay away from the side walls more. The cutter radius is more in contact with the material instead of the tips of the cutters, so the tool lasts longer. It also helps on cutter chatter, so we get better finishes. The ability to machine undercut cavities has also eliminated costly EDM work,” said M.R. Molds’ YASDA operator Mike Phillips.
“We realized a 75 percent reduction of hours on a stress ball cavity and core we recently built,” Finnie added. “The 5-axis mill allows us to reach all sides of a workpiece in one operation, including getting at difficult areas with shorter cutters, due to the ability to rotate the workpiece.”
“In the past we needed to make numerous set-ups and fixtures. We do not have to make nearly as many set-ups,” Finnie continued. “We also just purchased a robot for the machine and palletized tooling, providing automation that will propel our productivity and throughput even further. Our goal is to go fully lights out. “
Most importantly, holding tight flash tolerances, which was one of M.R. Mold’s biggest difficulties, is now a thing of the past thanks to the YASDA YBM Vi40.