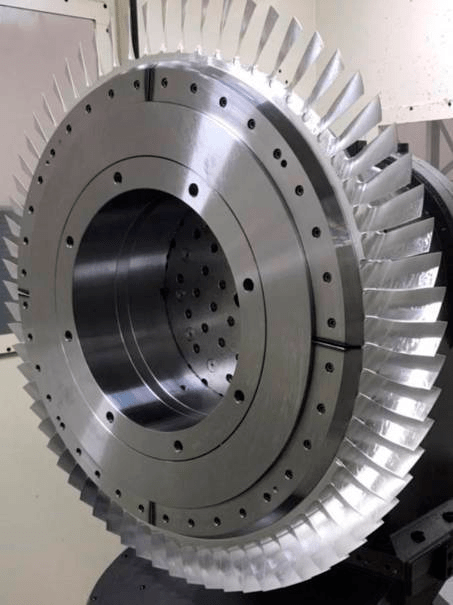
The extreme precision of CNC machining is needed for producing components such as this aerospace blisk.
The global aerospace industry, valued at over $800 billion, showcases the evolving power of innovation. In an industry where safety standards are non-negotiable, the production of aircraft components demands unparalleled precision and reliability.
Operating in the aerospace sector leaves no margin for error in your operations. From commercial airliners to fighter jets and satellites, the intricate systems within aircraft and spacecraft require components meet stringent industry standards of quality to prevent catastrophic failure from the slightest flaw.
Here we will explain how CNC machining is elevating the aerospace industry, and offer insights into best practices across critical areas of aerospace manufacturing such as quality control, planning, data security, traceability, and more.
Preparing for Aerospace Machining Jobs
For machine shops interested in aerospace machining, meticulous planning is the cornerstone of success. Precision begins long before the first tool touches the workpiece.
CAD/CAM for Design and Programming
Development of your workpiece begins with Computer-Aided Design (CAD) software, which enables aerospace manufacturers to create intricate component designs with unrivaled precision through Computer-Aided Manufacturing (CAM). CAD/CAM ensures the faithful translation of design intent into machine code and allows for real-time adjustments, reducing errors and rework while optimizing the efficiency of your machining.
Seamless integration with Computer-Aided Design and Computer-Aided Manufacturing (CAD/CAM) systems is crucial for efficient programming and production. Compatibility with industry-standard software can streamline the workflow and reduce the learning curve for operators.
Strategic Material Selection
Aerospace components are subjected to harsh environmental conditions, extreme temperatures, and intense stresses. Therefore, material selection is strategic and critical. Best practices involve choosing materials with exceptional strength-to-weight ratios, corrosion resistance, and fatigue properties. Balancing these factors is vital to ensure the longevity and reliability of aerospace components.
Tool Selection Strategies
In aerospace machining, tool selection is critical. Manufacturers must choose aerospace CNC equipment that is tailored to the specific material, component geometry, and machining process of each job. High-speed steel, carbide, and advanced coatings play pivotal roles in achieving optimal results, prolonging tool life, and enhancing overall machining efficiency.
Quality Control
Quality control in aerospace machining processes can’t be overstated. When safety is this critical, shops must leave no room for error and enforce stringent quality control practices.
Validation Processes for Quality Assurance
Aerospace machining requires rigorous validation processes to uphold the highest quality standards. These comprise comprehensive simulations, prototyping, and virtual testing to ensure that components perform flawlessly in real-world applications. Through advanced software and modeling techniques, manufacturers can identify potential issues before they arise, mitigating risks and enhancing reliability.
Inspection and Testing
The aerospace industry demands meticulous inspection and testing throughout the machining process. Precision instruments and cutting-edge technology scrutinize each component, verifying dimensional accuracy, surface finish, and material integrity. Non-destructive testing techniques, such as ultrasonic testing and radiographic inspection, play pivotal roles in detecting hidden flaws.
Compliance with Quality Standards
Adherence to aerospace quality standards and certifications, such as AS9100, is non-negotiable. The quality management system ensures manufacturers consistently provide products and services that meet customer, statutory, and regulatory requirements. Equally important, AS91000 ensures systems for process improvement. These standards set stringent criteria, ensuring that aerospace manufacturers consistently meet and exceed industry benchmarks.
Enhancing Efficiency and Productivity
Achieving optimal ROI for aerospace manufacturers is not just a goal, but a necessity. To stay at the forefront of innovation and cost-effectiveness, machine shops must constantly seek ways to optimize their processes, minimize waste, and reduce lead times.
Streamlining CNC Machining Processes
To boost efficiency, aerospace CNC manufacturers embrace process optimization. This involves fine-tuning every step, from design to final inspection. Implementing lean manufacturing principles and investing in advanced machining technologies, such as multi-axis CNC machines, accelerates production and maintains precision. Automating routine tasks also frees up skilled personnel for more complex work, further increasing efficiency.
Reducing Lead Times and Waste
Reducing lead times is essential to meeting tight project schedules. Lean practices, just-in-time inventory management, and advanced scheduling software enable manufacturers to deliver components faster. Additionally, minimizing waste through efficient material utilization and recycling programs conserves resources and contributes to cost savings.
Continuous Improvement
Continuous improvement is a mainstay in aerospace CNC machining. It incorporates a culture of ongoing evaluation and refinement. Regularly reviewing processes, seeking operator feedback, and investing in employee training are vital components. This commitment to improvement ensures that manufacturers remain agile, adaptable, and capable of meeting evolving industry demands.
Traceability: Tracking the Journey of Aerospace Components
Traceability serves as the indispensable thread that integrates complex component manufacturing. Traceability involves meticulously documenting and tracking the journey of aerospace components from inception to installation.
Importance of Traceability
The aerospace sector demands the highest level of quality control and accountability. Traceability ensures that every component’s history is recorded, enabling swift and accurate identification of production materials, processes, and personnel. In the event of a defect or failure, traceability is crucial for root cause analysis, recalls, and maintenance, ultimately upholding safety standards.
Implementing Traceability Systems
Aerospace manufacturers employ advanced traceability systems such as barcoding, RFID technology, and comprehensive databases to record every stage of a component’s lifecycle, from CAD/CAM designs and CNC programming to delivery. By integrating these systems into their operations, manufacturers can readily access transparent, detailed information about a component’s origin, materials, and manufacturing processes.
Data Security: Safeguarding Sensitive Information
The need for data security cannot be underestimated. With the evolution of technology and the increasing interconnectivity of manufacturing processes, safeguarding sensitive information has never been more crucial.
The Significance of Data Security
Manufacturers handle classified designs, proprietary algorithms, and sensitive customer data. Ensuring the security of this information is essential for protecting intellectual property and maintaining the integrity of aerospace components.
Any data security breach could lead to compromised designs, delayed projects, and potential safety risks, and financial losses; it is imperative to have robust data protection measures in place.
Best Practices for Protecting IP
Aerospace manufacturers must adopt best practices to protect intellectual property and sensitive data, especially when producing classified or proprietary components. This includes:
- Access controls, encryption, and multi-factor authentication to restrict unauthorized access.
- Regular security audits and employee training to mitigate internal threats.
- Secure data storage and transmission protocols should be employed to prevent leaks.
Compliance with Industry Regulations
The aerospace industry is subject to stringent data security regulations and standards, such as ITAR (International Traffic in Arms Regulations) and NIST (National Institute of Standards and Technology) guidelines.
Aerospace manufacturers must adhere to these regulations to maintain compliance and demonstrate their commitment to data security. Failure to do so can result in legal consequences and damage to reputation.
Key Considerations for Choosing the Right Equipment
Selecting the right CNC equipment is a pivotal decision for aerospace manufacturers, with far-reaching implications for productivity, quality, and profitability.
Precision and Tolerance Requirements
Aerospace components demand exceptionally high precision and tight tolerances. Manufacturers must carefully evaluate CNC machines’ capabilities in terms of accuracy and repeatability to ensure they can consistently meet requirements.
Material Compatibility
Aerospace components are crafted from a wide range of materials, from lightweight alloys to exotic composites. The selected CNC equipment should be compatible with commonly used materials, and offer the necessary cutting speeds and feeds without compromising surface finish or tool life.
Machining Capacity
As the size and complexity of aerospace components vary, manufacturers must assess the machining capacity of the CNC equipment. Evaluate factors, including work envelope, tool changers, and spindle speed, to ensure compatibility with the scale and intricacy needed for component production.
Advanced Features
Aerospace parts often involves complex geometries and intricate toolpath strategies. To tackle these challenges efficiently, the chosen equipment should offer advanced features such as multi-axis capabilities, simultaneous contouring, and high-speed machining options.
Total Cost of Ownership
Beyond the initial purchase cost, manufacturers must consider the long-term costs of ownership, including maintenance, tooling, real estate, and energy consumption. Investing in energy-efficient processes with readily available spare parts can contribute to cost-effectiveness over the equipment’s lifespan.
Developing the Necessary Skillsets
Skilled employees play a pivotal role and are essential to ensure precision, reliability, and safety.
To cultivate such expertise, aerospace manufacturers invest in comprehensive training and development programs for CNC operators and programmers. These programs cover a range of essential skills, including:
- Machine and equipment operation
- Proficiency in programming languages like G-code
- Precision measurement techniques
- Adherence to stringent safety protocols
Ongoing education is equally vital, allowing these professionals to keep pace with the aerospace industry’s evolving technologies and methodologies.
Moreover, staying current with industry trends is a necessity. CNC professionals must continuously update their knowledge to keep pace with advancements in materials, machining techniques, and digital technologies.
Industry-specific certifications and continuous learning opportunities ensure that skillsets remain aligned with the dynamic demands of aerospace production. Adapting and applying knowledge across diverse projects, from large-scale aircraft to miniature drone components, is essential in a skilled aerospace workforce.
Other Key Considerations
In addition to the critical factors previously discussed, there are other vital considerations that aerospace CNC machining firms must address to thrive in this competitive industry.
- Sustainability Practices. Sustainability is gaining increasing prominence in aerospace CNC machining. Manufacturers are under pressure to reduce their environmental footprint by adopting eco-friendly practices, according to a KPMG report. This includes minimizing waste, recycling materials, and optimizing energy consumption. Additionally, developing and using sustainable materials and processes are essential as aerospace companies strive to meet environmental regulations and respond to growing consumer demand for eco-conscious products.
- Supply Chain Optimization. To remain competitive, job shops and precision machining firms must focus on supply chain optimization. This requires efficient inventory management, just-in-time production, and strong supplier relationships. Optimized supply chains reduce lead times, lower costs, and enhance overall operational efficiency, ensuring manufacturers deliver parts on time and within budget.
- Navigating the Regulatory Landscape. Manufacturers in the aerospace sectors are heavily regulated, with strict standards and safety requirements. Companies must navigate a complex regulatory landscape, adhering to AS9100 and ITAR standards while staying informed about any changes or updates.
Ready to Seize Opportunities in Aerospace?
Aerospace job shops and mid-size precision machining firms can seize opportunities by implementing precision machining, nurturing a skilled workforce, and adhering to sustainability practices. This positions businesses to achieve excellence and innovation while satisfying demands and fostering a more sustainable industry.
Embracing emerging technologies, nurturing highly skilled teams, and staying agile in response to market dynamics will be essential for aerospace CNC manufacturing. Companies that embrace the opportunities will maintain a competitive advantage.
Methods partners with machine shops producing aerospace parts, taking their operations and profitability to the next level with the latest CNC solutions and custom engineering for your aerospace application.
Aerospace Tips
Modern Aerospace Machining Requires Dynamic Technology, Better Process Expertise
Learn how machine tool technology is adapting to the new demands and widening range of metals and materials being cut in aerospace machining shops.
Available Machines
Aerospace Machine Tools
We provide and engineer CNC machining solutions to deliver best-in-class accuracy, efficiency, and throughput for manufacturers producing aerospace components.