Synopsis: Beyond the CNC Skills Gap: Repairing Public Perception, Bridging the Labor Shortage, and the Path to Upskilling

Below is a synopsis of the full story. Unlock the full version.
There are a few grandiose questions that have vexed people for ages. Does free will exist? What’s the meaning of life? What happens when an unstoppable force meets an immovable object?
CNC machine shop owners and managers have long pondered an equally impenetrable problem: Where do I find skilled employees?
Finding and hiring capable staff is a chronic illness that the industry can’t seem to shake. Manufacturing employment has been declining for more than 40 years – from a peak of 19.6 million in 1979 to 12.8 million as of June 2019 – according to a November 2020 U.S. Department of Labor Statistics report.
Experienced machinists who are still in the industry may be poised to leave soon. Baby boomers, formally the largest generation in the U.S. at about 73 million people, will be at least 65 years old by 2030, according to the U.S. Census Bureau.
The industry is facing a wave of departures at a particularly trying time. Deloitte recently released a study estimating 2.1 million manufacturing jobs may go unfilled by 2030.
Like any other ailment, the first step to curing the skills gap plaguing the manufacturing industry is identifying the problem.
Diagnosing the Disparity
A skills gap is a clear difference between what abilities a company requires and what abilities employees have. While that’s undoubtedly part of the problem, another issue is the large number of aging workers exiting the workforce and the lack of younger employees interested in the trade.
The confluence of a traditional skills gap, retiring machinists, and the slow trickle of new employees is creating a multipronged problem. Invaluable knowledge is being left on the table. Machine shops cannot find the skilled employees they need to remain competitive or keep their doors open.
Courtesy of the U.S. Bureau of Labor Statistics
This is a synopsis of the full story. Unlock the full version.
Reshaping Public Perception
A skilled craftsperson in any trade – particularly an occupation as complex as a CNC machinist – is not born; they are created. That’s why teachers, machinists, and CNC enthusiasts across the country are trying to change the layman’s view of machine shops.
For the uninitiated, phrases “manufacturing facility” and “machine shop” conjure up the image of manual lathes, mills, presses, oil, grease, jumpsuits, and backbreaking labor. A 2017 study backed by Deloitte and The Manufacturing Institute surveyed 1,000 Americans in 50 states found that less than 50% of respondents believe manufacturing jobs are “interesting, rewarding, clean, safe, stable and secure.” However, about 80% of survey respondents view U.S. manufacturing as vital to economic prosperity, and 88% believe future manufacturing jobs will require high-tech skills.
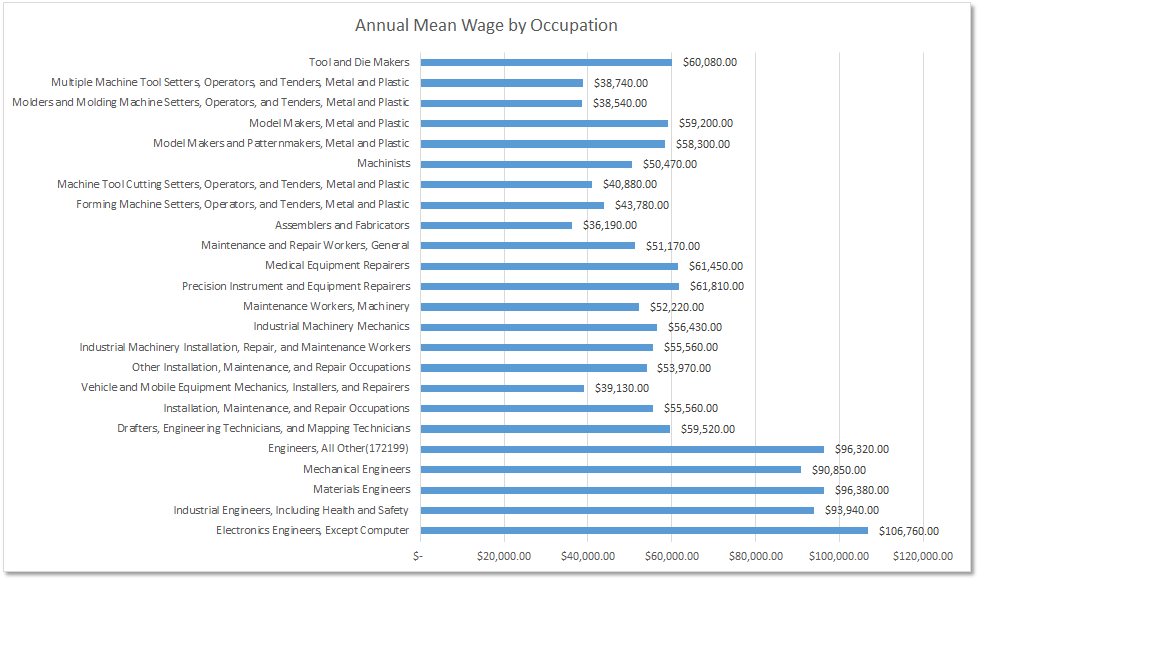
Annual Wages in the Manufacturing Industry by Occupation.
Annual wages have been calculated by multiplying the corresponding hourly wage by 2,080 hours.
Source: U.S. Bureau of Labor Statistics
This is a synopsis of the full story. Unlock the full version.
Assembling Interest
Generating interest in CNC machining is one of the first steps to bridging the workforce and skills gaps. When new employees enter a machine shop, owners and managers will be able to upskill existing machinists.
That’s why industry enthusiasts are using every available end-mill in their metaphorical tool changer to spark the curiosity for CNC machining in younger generations.
Widening the Target Audience
Educators not only have to get through to students–parents and guidance counselors also need to know that someone can have a fulfilling, prosperous career as a skilled CNC machinist. Machinists and operators readily recalled some of the reasons they were interested in CNC machining – problem-solving, programming, seeing the fruits of your labor as a physical component, and figuring out how to make more parts faster.
Filling the Gap
One machine shop decided to take matters into their own hands. Carl Pasciuto, the president of The Custom Group and co-owner of Custom Machine, a machine shop based in Woburn, Mass., had exhausted every possible route to find skilled labor. He was tired of wasting resources trying to find qualified candidates.
So, in 2008, the family-owned business launched a CNC operator pilot program aimed at basic education. In 2010, they became an accredited vocational school, The Center for Manufacturing Technology (CMT).
“What we’re finding is that the people coming into our traditional training programs are really green,” said Joanna Dowling, Director of the vocational school and Carl Pasicuto’s sister. While the industry needs as many people as it can get, Dowling said, and training/vocational schools produce entry-level employees, those new workers still need time on the shop floor with experienced professionals.
“That’s where the gap is–the time it takes for the learning to resonate with what machine shops are actually looking for,” she said.
Answers Through Automation
Automation can allow machinists to apply that knowledge better. Solutions such as automated cells, automatic pallet changers (APCs), and automatic tool changers (ATCs) can free up machinists to work on other tasks to improve spindle utilization.
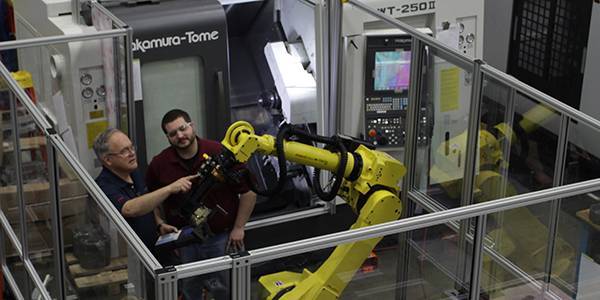
Automation systems alleviate CNC machine shops by increasing cycle times, throughput, and allowing skilled machinists to tackle more complex tasks.
According to Zachary Spencer, Automation Manager, Robotics at Methods Machine Tools, that aspect of automation alone brings some benefits.
“It’s tedious work, its repetitive, and people don’t really like to do it,” he said. By eliminating monotonous tasks such as loading, unloading, and changing parts and components, employees are more engaged on the shop floor.
If a part has a relatively quick cycle time of two or three minutes, an operator could be tending that machine for hours, removing the part, clearing chips, changing tools, and finally preparing the next piece to start the cycle over.
Manufacturers Wanted
There is no one-size-fits-all answer to addressing the skills gap, but there are solutions that work. Advanced automation systems can increase throughput while allowing skilled machinists to handle complex tasks. To address the immediate need for talent, machine shop owners and managers can invest in their employees. Upskilling the existing workforce will spread the wealth of knowledge around.
To address the long-term issue of the labor shortage, the manufacturing industry has to reshape its image. That involves educating students, teachers, parents, guidance counselors – and anyone else who will listen – about the rewarding aspects of CNC machining. According to Brian Norris, Director of the Northeast Advanced Manufacturing Consortium, informing the soon-to-be-employed, underemployed, or unemployed about the wide range of options they have in manufacturing and machine tooling is the perfect starting point.
“Manufacturing wants you, they want everybody,” he said. “They want anybody who will show up for work, is willing to learn, and takes pride in what they do.”
This is a synopsis of the full story. Unlock the full version.