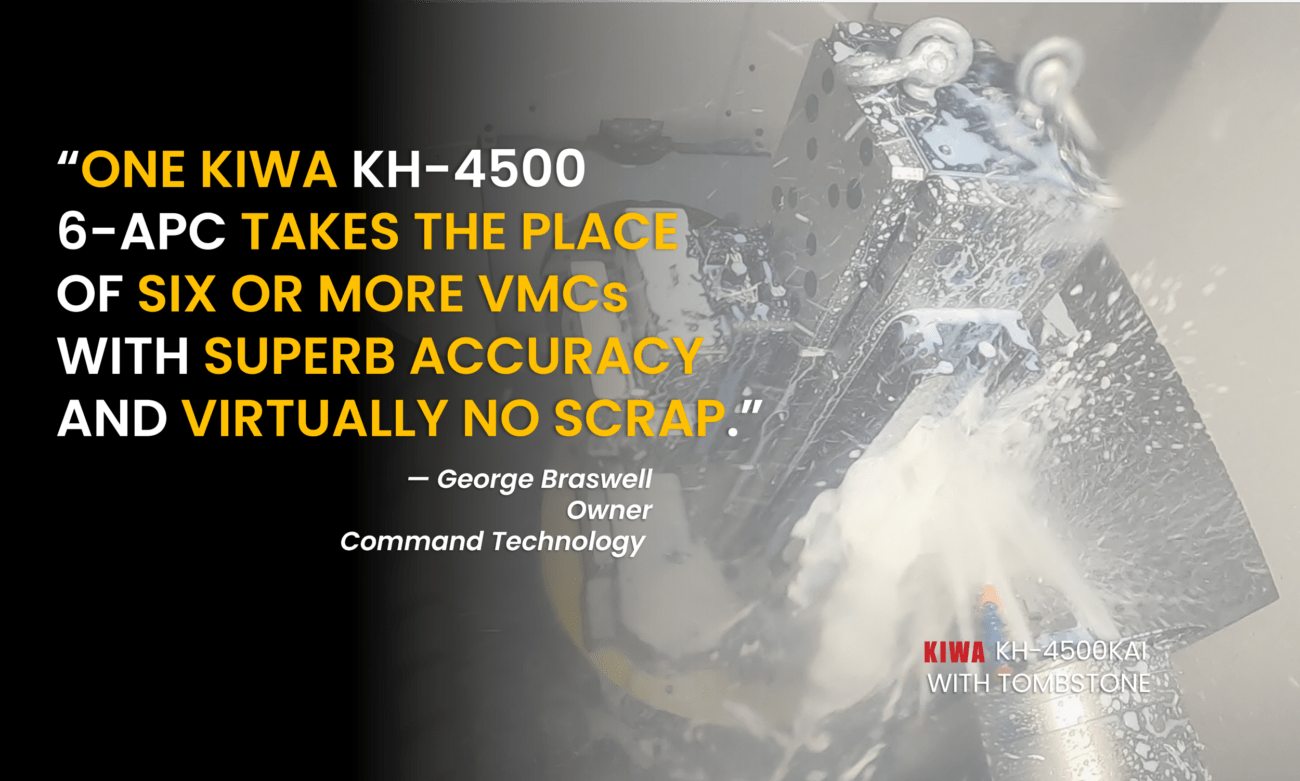
Case Study
Command Technology
RequestInformation
Problem
Slow and costly process of bonded assembly that is required for aerospace customers.
Solution
New machines and equipment to increase production by decreasing downtime, waste, and assembly
Results
• Reduced time and cost by 60% per assembly.
• All assembly components were now being machined simultaneously in just one machine cycle.
• Mostly unattended second, third, and weekend shifts were added to production.
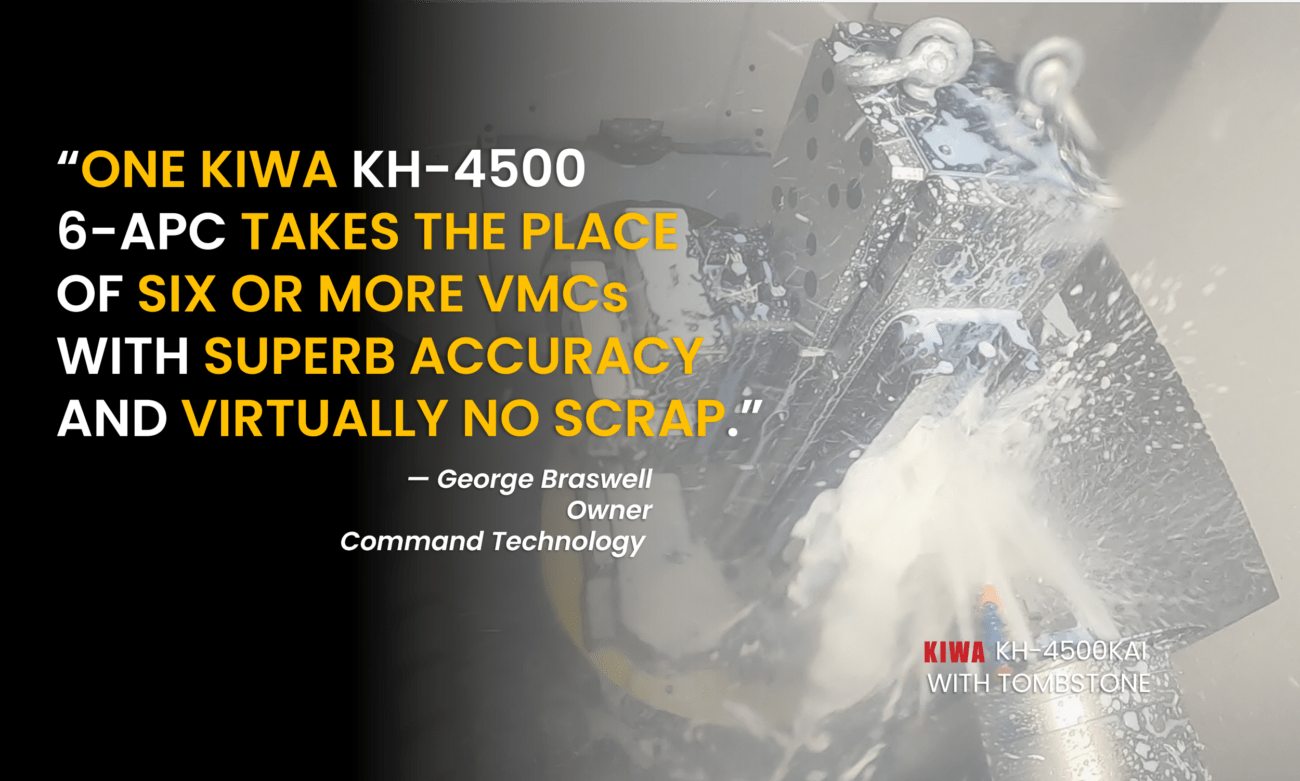