CNC automation technology continues to transform the automotive industry along the entire production chain, from raw materials suppliers all the way to the final assembly line.
Thanks to automated CNC machining, Tier-1, Tier-2, and other suppliers can deliver higher quality automotive parts to other suppliers or OEMs faster.
Efforts to improve the quality and efficiency of parts machining have continued as engineers at companies like Methods partner with machine shops to integrate new equipment for automated tool-changing, material handling, robotic cell operators, real-time monitoring, and more.
Automated automobile manufacturing incorporates CNC technology, integrated technology, and flexible automation. This article focuses on how the latest automated CNC solutions are giving precision manufacturers a competitive advantage in the automotive industry.
The State of Automation in Today’s Automotive Industry
The automotive industry is arguably the biggest adopter of automation technology. In fact, the automotive sector accounts for nearly half (47%) of all industrial robotics sales in North America.
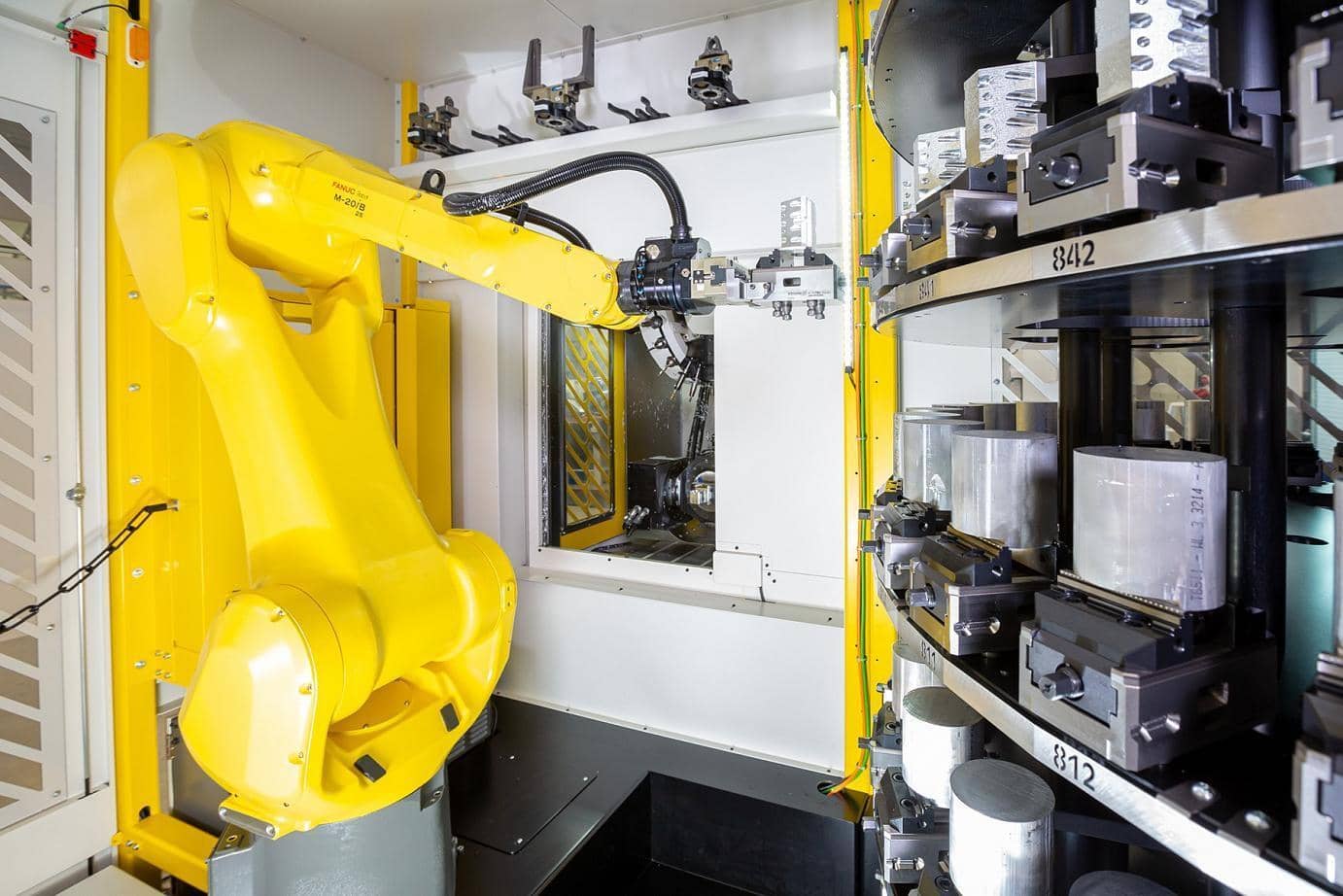
Methods’ Plus Big-K Automation Solution featuring FANUC RoboDrill
According to a forecast report by Technavio, the automation market share in the automotive industry is expected to increase by $1.95 billion from 2021 to 2026, and the market’s growth momentum will accelerate at a CAGR of almost 4%.
CNC automation combines several different machining operations, including turning, milling, and drilling, to produce vehicle components with precision and high repeatability while creating efficiencies by reducing the manufacturer’s reliance on human interactions and multiple setups.
Automotive Parts Produced by CNC Machines
Automation systems increase production efficiency for these and other automotive parts:
- Engine components – camshafts, cylinder heads, crankshafts
- Drivetrain components – gears, shafts, axles
- Suspension components – control arms, springs, shock absorbers
- Brake components – rotors, calipers
- Exhaust components – manifolds, mufflers
- Fuel system components – injectors, fuel rails
Due to the intricate workflows involved with modern automotive assembly, incorporating automation into the production of individual components still often requires some human involvement to oversee and control end-to-end operations.
Automation Goes Beyond Robots and Conveyors
Robotic arms and chip conveyor systems only scratch the surface of automation possibilities for auto suppliers.
Tool Changing
A fully integrated robot quickly and accurately switches between different cutting tools from a magazine during machining.
What are the benefits of automated tool changing?
- Minimizes the risk of tooling errors, such as incorrect tools used
- Eliminates the time and effort required to change tools manually
- Reduces manual intervention and the risk of workplace accidents
- Adds flexibility for using a wider range of tools
Material Handling
Integrated robots, conveyors, automatic pallet changers, and automatic storage and retrieval systems move raw materials, semi-finished products, and finished products. Automation systems may be used on a single machine or within a machining cell when multiple operations are necessary.
What are the benefits of material handling?
- Increases productivity by reducing time and effort for manual material handling
- Minimizes risks of material handling errors, such as incorrect positioning or damaging workpieces
- Maximize floor space for efficient storage and retrieval of materials
- Eliminates the need for manual intervention and reduces the risk of workplace accidents.
Automation Options for Automotive Suppliers
The automotive manufacturing process is highly diverse. As such, different types of CNC automation solutions will provide more value for certain automotive machining applications. These types of automation include:
- Automating Existing Equipment – CNC equipment that is still far from its end-of-life can benefit from the investment in automation solutions that optimize tool changing, material handling, and other processes integral to automotive parts machining.
- Custom Turn-key Solutions – Turnkey automated CNC solutions can be developed and customized for a particular automotive application. These are complete, integrated systems that provide everything needed for producing automotive parts, from the machines and automation equipment to the software and training materials.
- Automating Machine Components – Various CNC machines use certain tools and components for specific applications that can be automated when manufacturing automotive parts. For instance, Lathes create pieces from various materials, including metals and plastics. Milling machines cut and shape materials using a rotating cutting tool to create intricate designs and shapes. Other machines under this category include routers, laser cutters, and plasma cutters.
- Automated Production Cells – Production cells streamline the automated machining process and minimize setups. They also reduce downtime, increase efficiency, and improve the final product quality. Automotive suppliers can integrate these cells with other production systems, such as ERP systems, to enhance communication and collaboration between different departments and stakeholders.
Advantages and Benefits for Automotive Applications
Leading automotive OEMs, and Tier 1, 2, and 3 suppliers are rapidly implementing CNC automation for the many production benefits that deliver a competitive advantage. These benefits can’t be overstated, and include:
Removing Pain Points and Bottlenecks
With CNC automation, vehicle manufacturers and automotive suppliers can solve their common pain points and eliminate production bottlenecks:
- Production Planning – Systems manage production schedules, track the production progress, and allocate resources in real-time.
- Production Set Up – Perform multiple setup procedures simultaneously, freeing up resources for other tasks and improving overall production efficiency.
- Workpiece Loading and Handling – Load and unload workpieces consistently and accurately, enabling repeatable and reliable production processes.
- Traceability – Collect and store production data in real time, creating a comprehensive and accurate record of the manufacturing process to meet manufacturer and regulatory requirements.
Faster Production Speeds
Speed ranks among the top benefits when incorporating next-level CNC machine solutions in the automotive industry. Automation of part production eliminates fatigue and the need for lengthy and labor-intensive manual machining that can slow down the manufacturing process. Greater speeds increase CNC automation’s benefits when producing low-mix, high-volume automotive parts.
Accuracy and Precision
The automotive industry demands high-level accuracies alongside acceptable tolerances that eliminate the malfunction of critical car parts. Autonomous CNC machining removes the risk of human errors, leaving little for defects. The finest machine settings can provide tolerances of ±0.001.
Improved Repeatability
Beginning with CAD, automation ensures consistent processing parameters by storing and reusing tool paths to ensure each piece is produced congruently.
Project Customization
Automation handles a range of parts and quantities better, providing fast and more effortless programming, real-time adjustments, and increased scalability.
Cost Reduction
While the initial cost of acquiring and automating CNC equipment might be high, the benefits compensate for that investment. Greater production capacity offers opportunities for new business or diversifying into other industries. Operational efficiencies, increased production capacity, and higher quality also factors into calculating the ROI of automation solutions.
Common CNC Automation Solutions
Other than manufacturing components and parts for vehicles, automated CNC machining equipment offers even more possibilities for automotive parts suppliers:
- Tool-changing systems – An automated tool-changing system improves a CNC machine’s production and tool-carrying capacity, changing tools quickly without the need for a manual operator.
- Pallet changers – A CNC robotic arm with actuators and grippers clamp and release the workpiece from a storage system or rack that holds numerous workpieces. It typically consists of a programmable logic controller (PLC) or a computer numerical control (CNC) system.
- Automated part loading and unloading systems – These systems automate the process of loading and unloading parts onto the machine, reducing the need for human intervention and improving spindle time.
- In-process gauging – This real-time system eliminates guesswork and reduces opportunities for error when measuring between cutting passes.
We Specialize in CNC Automation for Automotive Parts Manufacturing
Methods offers CNC machining solutions capable of supporting even the most complex automation projects for automotive manufacturers and suppliers.
We partner with the world’s leading machine builder brands, including FANUC, Kiwa, Nakamura-Tome, OKK, and Yasda, to bring you automation solutions customized for your automotive production needs.
Contact our engineering experts to see how Methods can help you produce the highest quality automotive parts faster and with unmatched precision.
FAQs
- Minimizes the risk of tooling errors, such as incorrect tools used
- Eliminates the time and effort required to change tools manually
- Reduces manual intervention and the risk of workplace accidents
- Adds flexibility for using a wider range of tools
- Increases productivity by reducing time and effort for manual material handling
- Minimizes risks of material handling errors, such as incorrect positioning or damaging workpieces
- Maximize floor space for efficient storage and retrieval of materials
- Eliminates the need for manual intervention and reduces the risk of workplace accidents
- Detect defects, deviations from specifications, and machining malfunctions
- Increase efficiency by measuring and ensuring exact positioning
- Provide real-time feedback on process parameters, such as tool wear and cutting conditions
- Offer increased versatility for controlling a wider range of CNC machining processes
- Alert machine operators of potential dangers and defects, increasing safety and reducing equipment damage
- Minimizes the risk of errors and improves accuracy
- Provide real-time feedback on process parameters, such as tool wear and cutting conditions.
- Production planning – Systems manage production schedules, track the production progress, and allocate resources in real-time
- Production set up - Perform multiple setup procedures simultaneously, freeing up resources for other tasks and improving overall production efficiency
- Workpiece loading and handling - Load and unload workpieces consistently and accurately, enabling repeatable and reliable production processes
- Traceability – Collect and store production data in real time, creating a comprehensive and accurate record of the manufacturing process to meet manufacturer and regulatory requirements.