The Benefits of 5-Axis CNC Machining
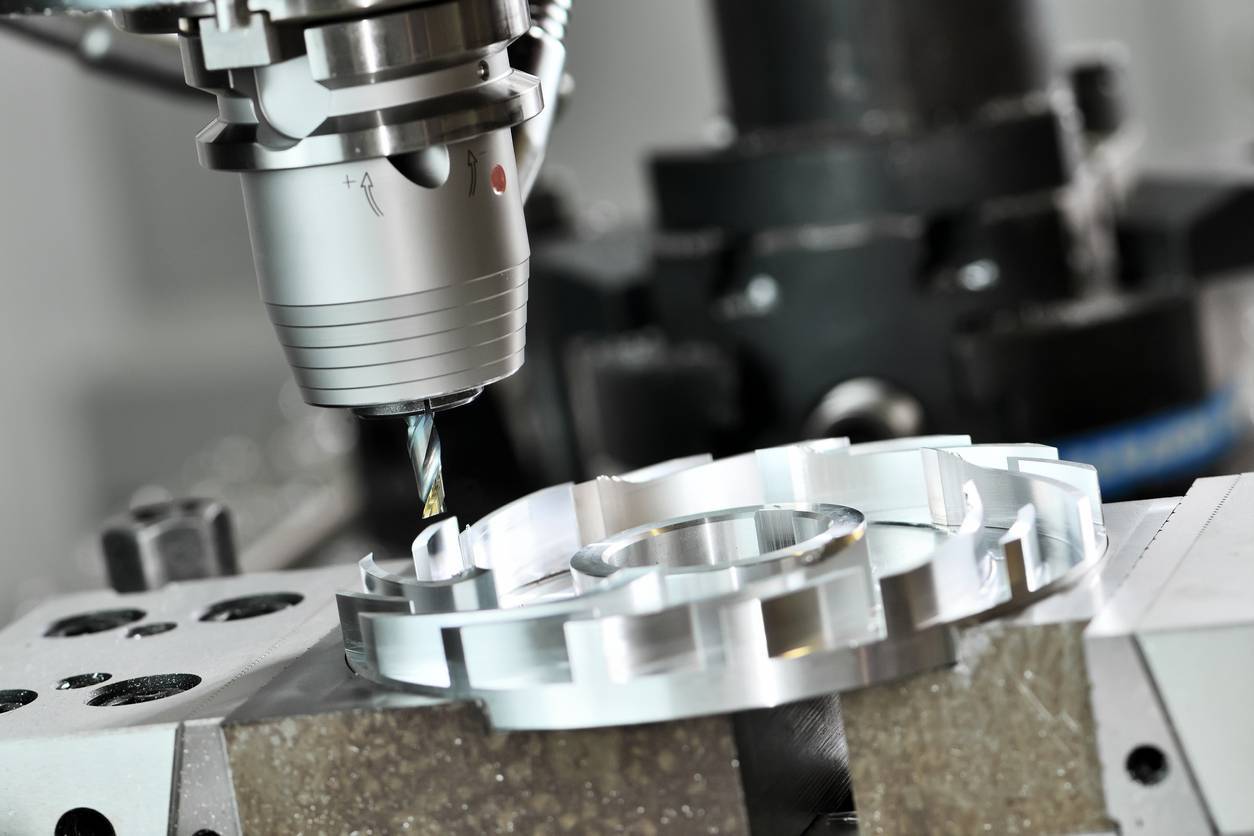
In the precision manufacturing industry, machining technology continues evolving from punch-controlled 3-axis CNC machines to more sophisticated 5-axis machining solutions.
A report by Technavio has projected the 5-axis CNC machining market to grow at a compound annual growth rate of nearly 6% between 2021 and 2025, citing Methods partner FANUC as a leading 5-axis machine manufacturer.
The need for self-optimized machine cutting is one of the significant factors driving this growth in 5-axis machining, in addition to higher accuracy and greater precision for tighter tolerances, and increased efficiencies for automated operations.
Shop owners should consider 5-axis solutions when evaluating their current lineup of machines and operations. The benefits delivered by 5-axis machine tools can offer shops a competitive advantage through optimum cycle times, precision, and overall customer satisfaction.
What are the Five Axes in 5-Axis CNC Machining?
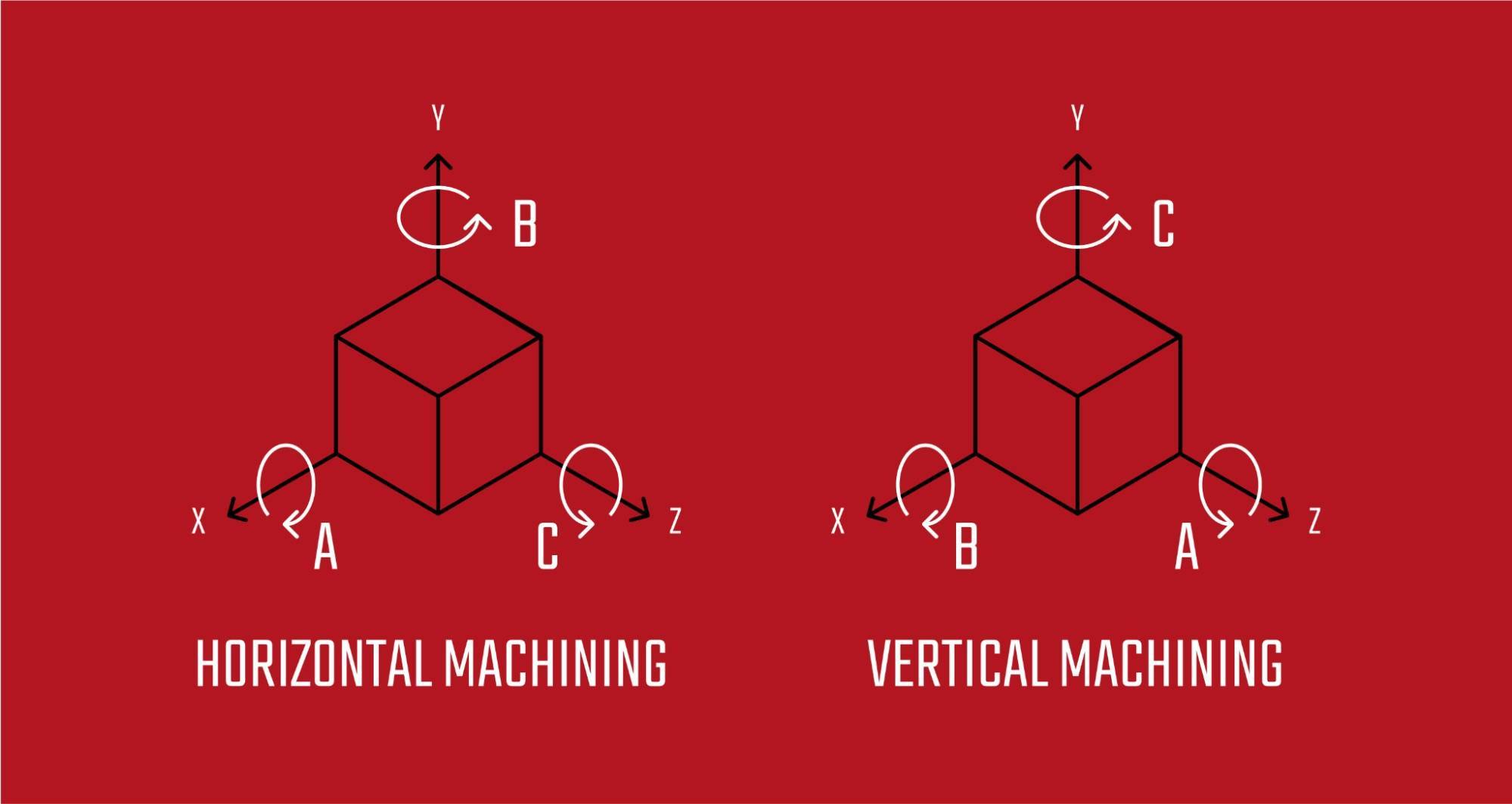
The five axes are labeled differently for horizontal vs. vertical CNC machines
A CNC axis count refers to the number of directions a CNC machine tool can move to produce desired parts.
Here are the five axes upon which a 5-axis machine tool can move:
- X-axis
- Y-axis
- Z-axis
- A-axis
- B-axis
Take the case of conventional 3-axis CNC machines, which naturally have a three-axis count. 3-axis machines can move sideways on the X-axis, up and down on the Y-axis, and back and forth on the Z-axis.
Beyond the three linear axes, 5-axis CNC machines add two axes, typically called the A-axis and B-axis. These two additional axes enable 5-axis machines to tilt and rotate the cutting equipment or parts to produce more sophisticated geometries than 3-axis machines.
These make 5-axis machines the secret to producing highly precise components without seams or signs of welding. 5-axis machining capabilities have transformed manufacturing industries, such as automotive, healthcare, aerospace, and agriculture.
6 Benefits of 5-Axis Machines
Investing in 5-axis CNC machining produces greater productivity and improves numerous manufacturing metrics, delivering a measurable and significant ROI through these advantages:
1. Higher Precision and Accuracy
5-axis CNC machines operate with greater precision to deliver accurately machined and smoother parts that would be too complex for machining on traditional 3-axis CNC equipment.
2. Improved Production Speed (Lead Times)
The tangential arrangement of the cutting tools to the material removes more material with each rotation. When 5-axis tools are combined with the machine’s single setup, cycle times improve significantly.
3. Fewer Setups
With 5-axis machines, you can set up your workpieces at one time to handle all milling operations needed to fabricate complex geometries. You’ll produce parts faster, minimize operational costs, and reduce most errors prevalent in conventional 3-axis machines.
4. More Complex Part Geometries
The ability of 5-axis CNC machining to move workpieces over more dimensions without removing them gives it a significant advantage over conventional 3-axis machining. These machines attack the most complicated angles to create complex geometries with premium finishes with tighter tolerances.
5. Better Surface Finishes
The fourth and fifth axes (A-axis and B-axis) on 5-axis machines bring the work material closer to the cutting tool. Shorter cutting tools produce better surface finishes because the shortened length makes them less susceptible to machining vibration.
6. Improved Drilling Capabilities
5-axis machines change the game for drilling applications because of the additional axes that allow the machine to reach tighter and more complex angles, producing parts with finer finishes.
Industries Using 5-Axis Equipment
Various industries rely on shops with high-performance 5-axis CNC machines to produce sophisticated parts requiring tight tolerances.
- Aerospace – Typical aerospace components produced by 5-axis CNC tools include valves and turbine blades requiring precise execution on complex geometries.
- Automotive – The high throughput of 5-axis equipment make these machines ideal for the low-mix, high-volume production needed for the automotive industry while maintaining the highest quality.
- Medical – Medical instruments, implants, devices, and equipment parts must meet strict quality standards. The ability of 5-axis machines to produce the necessary quality at greater speed and the highest accuracy gives medical component manufacturers greater confidence.
- Energy – The oil and gas production industry requires parts produced from extremely hard steels and exotic alloys using 5-axis machines. The complex components that energy equipment needs. Such parts include wind turbines and compressor blades.